The Role of Forming Fabric in Improving Paper Quality
The woven medium which is used to drain water in the forming zone of a modern paper machine is called the forming fabric. This is notable since the final properties of the finished product as well as the costs and overall efficiency are highly influenced by the internal structure and surface topological characteristics of the forming fabric. As we move towards a more technologically advanced understanding of forming fabric, a deeper understanding of its properties will be known.
Topological characteristics of the Forming Fabric surface
The dependability of paper quality and the surface topology of the forming fabric is no mystery to the pulp paper industry. During the forming process of paper production, the knuckles in the pattern of the forming fabric create areas of low density in the paper while the holes in the surface allow for a high-density area in the fibre web. The difference in these micro densities directly relates to ink penetration and spread, half dot and skip dot tests and gloss.
In contrast to modern style fabrics, older iterations have a visible wire mark of the twill of the fabric weave. As technology advances, the micro densities become even more minute with the industry transitioning from single layer to double layer, to extra-support, to Triple Layer and SSB. Each iteration has a better top surface fineness and increased fibre support of the forming fabric.
And this is quite beneficial as the modern concern for recyclability and increased recycled content has caused the fibres to become quite short. The modern-day SSB fabrics offer a finer product with reduced micro densities across the sheet surface.
Internal structure
Paper Machine clothing suppliers have poured in a ton of efforts and resources to understand more about the internal structure of the forming fabric. As more and more modern complex looms come into the scene equipped to take on complex weave patterns, the opportunity to engineer the internal structure of the forming fabric is becoming more and more a reality.
The modern SSB Class of forming fabrics come in three variants based on their internal structure. These include:
- SSB (Weft Bound)
- SSB (Warp Bound)
- SSB (Warp Intrinsic)
Although each of these has a plain weave top surface, there is a considerable difference in their internal structure. Recent reports from Paper machine clothing companies indicate the fact that the behaviour of the internal structure relative to the drainage pressure can have an impact on the machine operations and in turn the quality of the paper. It shows that with more open structures, drainage pressure resistance is quite negligible. On the other hand, more complex structures offer a higher degree of resistance to drainage pressure.
Suppliers are measuring an estimate of the drainage pressure resistance since the interior structure’s “Hour Glass” structure and minimal openness determine how resistant it is to drainage pressure. While some vendors depend on computer modelling, others use empirical techniques in the lab to test the resistance to drainage and water drainage rates. To accurately measure this impact, a solid standard parameter has to be developed, but there is still work to be done.
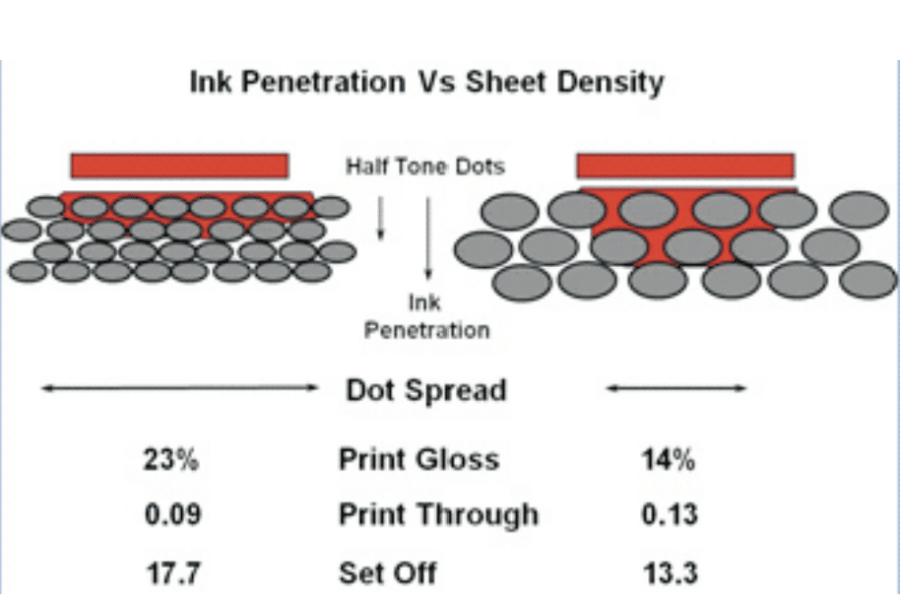
SSB (Weft Bound)
This is perhaps one of the most common internal structures you can find nowadays. SSB offers fast drainage thanks to its open structure in the centre plane which also helps to avoid fibre embedment making for a very fine top surface.
SSB (Warp bound)
The top and bottom layers of the forming fabric are joined together by this structure’s application of Top MD yarns. The middle plane of this structure is quite open, allowing for extremely quick drainage. Once more, the top surface is very thin to prevent fibre embedment.
SSB (Warp Intrinsic)
The top surface plain weave of this structure is made using all the MD yarns. This structure, which is more intricate towards the plain’s centre, offers resistance to early impingement drainage. Less fibre embedment results from the slower initial drainage, which ironically results in enhanced drainage after the initial impingement.
These grades have plenty more variations used by the people which offer different warp and weft ratios like 1:1, 2:1, 3:1 etc. In addition, these differences in warp and weft ratio influence the fabric’s response to drainage pressure, albeit to a lower extent than the 3 categories.
Many operational difficulties associated with considerable expenditures are impacted by the variations in internal structure amongst SSB fabrics. The following are some of the significant effects that have been observed:
- Fibre usage
- Machine Speed
- Drive load
- Chemical usage
- Refining / Furnish mix
- Downtime / Total efficiency
Some of the important implications of creating internal fabric structure on observable paper web characteristics
- Sheet strength/stability
- Z-direction distribution of fines
- Micro-density profile
- Smoothness / 2-sidedness
- Mechanical filler retention
The vacuum demand and drainage behaviour of the forming fabric are both significantly influenced by the internal structure of the material. The fabric drive load is affected by the vacuum demand, and the fabric is subjected to higher abrasion on the machine side. Machine speed, raw material quality, supply quality, and other process parameters will help in determining the best forming fabric for improving the paper quality.
Parting words
The efficiency of the paper machine, as well as the paper quality, is quite influenced by the forming fabric’s internal structure and topographical characteristics. Therefore, understanding the interactions and relations between structures, drainage, and quality is crucial to getting the desired benefits which also encourages closer collaborations between paper makers and suppliers of fabric.
The industry is going through a lot of changes and reforms in tech. Stay in tune with all the latest happenings in the industry with the Coniferous. One of the country’s leading paper suppliers and ardent contributors to the pulp and paper sector. Tune in to Coniferous for a dose of all things green.