A glimpse into the world of paper cups
Paper cups are one of the most commonly used disposable items in the world. You can find them in restaurants, homes, offices, schools and just about everywhere else. But what many people don’t know is that there is a hidden world of paper cups that exists beyond their everyday use.
In this blog post, we will explore the different types of paper cups along with the process of paper cup making.
How is paper and paper cups are made?
Most food, refreshments, and snacks are supplied in paper packaging, demonstrating how important paper is in our daily lives. I’ll walk you through how trees are made into paper in the sections below.
- Pulp Production
After being cut, trees are debarked and turned into wood chips, which are then processed into pulp using a mechanical device. The pulp is put through the digester, where it is cooked in a chemical solution including sodium hydroxide and sodium sulphide at a high temperature.
- Beating
The residual pulp is pounded and squeezed at this stage of the process. Different filler materials, like clays, chalks, or chemicals like titanium oxide, can be introduced during this process, and these additions will affect the opaque nature and other aspects of the finished product.
- Paper from Pulp
The pulp is spread out and passed through a mesh screening system, where it is crushed by a succession of rollers to assist in removing water.
After the water has been removed and the pulp has been pressed, the paper is passed through a succession of steam-heated cylinders to assist eliminate any leftover moisture before being wound onto enormous reels. The paper is flattened and compressed even more by feeding them through calendars, which are metal rollers. The paper could be further treated by running it through a size vat to get a coating that can be brushed on or rolled on. For instance, when producing paper cups, this covering may be plastic.

The Types of Paper Cup
Normal paper cup: Wood, a renewable resource, is the primary raw material used by paper manufacturers. The paper used in regular cups can originate from jungles all around the globe, like the Amazon, but it could also come from European forests that meet FSC requirements but are not certified.
- FSC paper cup
When an item or paper is labelled as FSC recognized, it signifies that the entire production line has been validated, including the producer, distributors, and suppliers. The FSC organisation has 10 principles that must be followed in forestry, such as harvesting no further trees than what the forest itself can renew, ensuring a steady supply of material.
- FSC 100%
This indicates that the product’s wood is sourced from FSC-certified and well-managed forests.
- FSC Recycled
All of the wood or paper used in the item has been salvaged or re-used.
- FSC Mix
This indicates that the product is created from a combination of recyclable materials, FSC-accredited forests, or managed timber.
- FSI Paper
Fibre Sorting, Inc. (FSI) is a paper manufacturing company that has been in business for over two decades and produces paper products entirely from recycled resources. FSI employs 100 per cent recycled paper as a raw resource, and the firm collaborates with wastepaper vendors in the Philippines to provide a stable and dependable source of raw materials.
What is the process for paper cup making?
After the paper is done, it is transferred to various facilities and companies for various uses, one of which is the creation of paper cups.
When it comes to making paper cups, there are three or four phases. The number of stages depends on whether they are printed or otherwise; if they are printed, they are printed before being carved out and pleated into paper cups. This is also why printing on paper cups that have previously been folded is nearly impossible. After the paper cups have now been printed, the cups are cut out in slightly bent templates and then fed through a large machine that curls and folds the tip of the cup to make it comfortable to drink from. In the last process, the bottoms of the paper cups are inserted and reinforced to strengthen the cup’s structure.
- Offset Printing
Offset printing is among the most often utilised printing processes for paper cups, particularly when printing in big quantities. The printing plate is the costliest aspect of offset printing. The efficient method also assures reasonable pricing, which will decrease as the volume is increased.
- Tampon print
Tampon printing is comparable to the ‘stamping’ method, in which ink is transferred from an engraved metal plate to a flexible pad, which is then pressed onto the item to be printed.
- Flexographic printing
Flexographic printing is a newer variant of letterpress that can print on nearly any sort of material, like paper, plastics, metals, and even cellophane.
- Printing on a computer
Digital printing, often referred to as “printing,” is one of the most frequent and effective techniques of printing colour images or text onto paper or another substance.
Digital printing is increasingly commonly employed in newspapers since it is faster and less expensive when publishing articles with many distinct designs in small numbers.
Paper cup coating
- PE – plastic coating paper cups
Most paper cups include a thin coating of plastic within the cup that keeps it together and keeps it from seeping. The plastic-coated paper cups are manufactured of PE-plastic, which implies the plastic is manufactured of naphtha, an oil by-product.
- Paper cups with PLA – Bioplastic
PLA paper cups, like every other type of paper cup, have a thin layer of plastic within the cup, but it is distinct from the others. PLA is manufactured from plant-based resources including sugar, maize starch, cassava starch etc.
- Cups made with paper instead of plastic
Because of the public outcry over plastic trash and non-recyclable paper cups, policymakers, corporations, and producers had to respond quickly and come up with a great solution to eliminate plastic waste. Therefore, the idea of plastic-free cups was born, and it is now a reality.
Water-based dispersion is used on both sides of the coating to allow liquids to be contained, while chemithermomechanical pulp is used in the cup’s centre layer.
Innovations around paper cups
System of recycling improvement
The plastic coating jams the filters at the paper mills, preventing paper cups from being recycled. The United Kingdom has expanded from one tiny paper recycling plant to two and is currently constructing the world’s largest paper recycling lines.
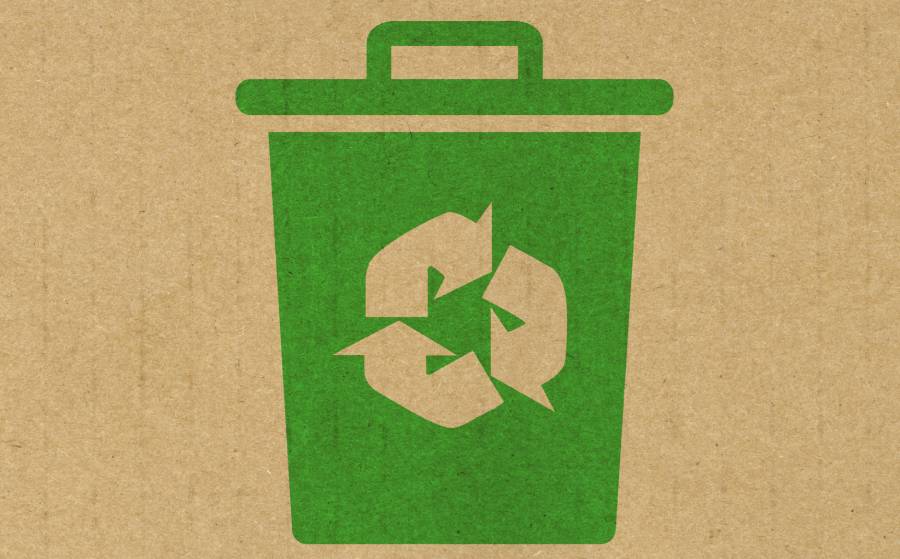
Meanwhile, coffee houses have taken it upon themselves to fund coffee cup containers where customers may discard their used cups, making it easier to segregate paper cups from regular trash and making it easier for recycling plants to collect the
What are coffee shops up to these days?
Starbucks and environmental charity Hubbub established a £1 million fund to reduce paper cup waste. To achieve this, they will use the funds to help extend and improve paper cup recycling facilities across the UK and other nations.
To assist reduce paper cup waste, the UK’s largest coffee businesses, including Costa Coffee, Pret a Manger, Greggs, Starbucks, and Café Nero, are offering discounts to customers who carry their cup rather than using a throwaway cup.
Paper cups that are CO2 neutral
Whenever we say paper cups have a big impact on the environment, we also mean the CO2 they generate during production, transportation, and decomposition. This section will discuss how CO2 neutral paper cups can be achieved.
Regrettably, it is not possible to manufacture and transport paper cups that do not emit more CO2, necessitating the completion of other operations for the paper cups into becoming CO2 balanced. Planting more trees, assisting individuals with isolating their homes so they consume less energy, or a third alternative that is CO2 positive are some of the activities that these organizations/companies engage in.
Coffee mugs made from natural, biodegradable materials
A creative design firm is attempting to reduce plastic waste by ‘growing’ coffee cups from fruit.
They’re constructed from gourds, which are like pumpkins in appearance, and are ‘grown’ inside to take on the shape of a coffee cup. The concept derives from our forefathers’ use of fast-growing squashes for storing liquids and drinking water. Everything about these cups is entirely natural. To make varied sizes, they 3D-print moulds and place them inside baby gourds, allowing them to grow, then removing the moulds and allowing the gourds to dry. Gourds require 3 weeks to fruit from the day they are sown, and they’ll need to stay outside and dry for four months before they can be utilised.
Learn more about the other disposable tableware that is commonly used.